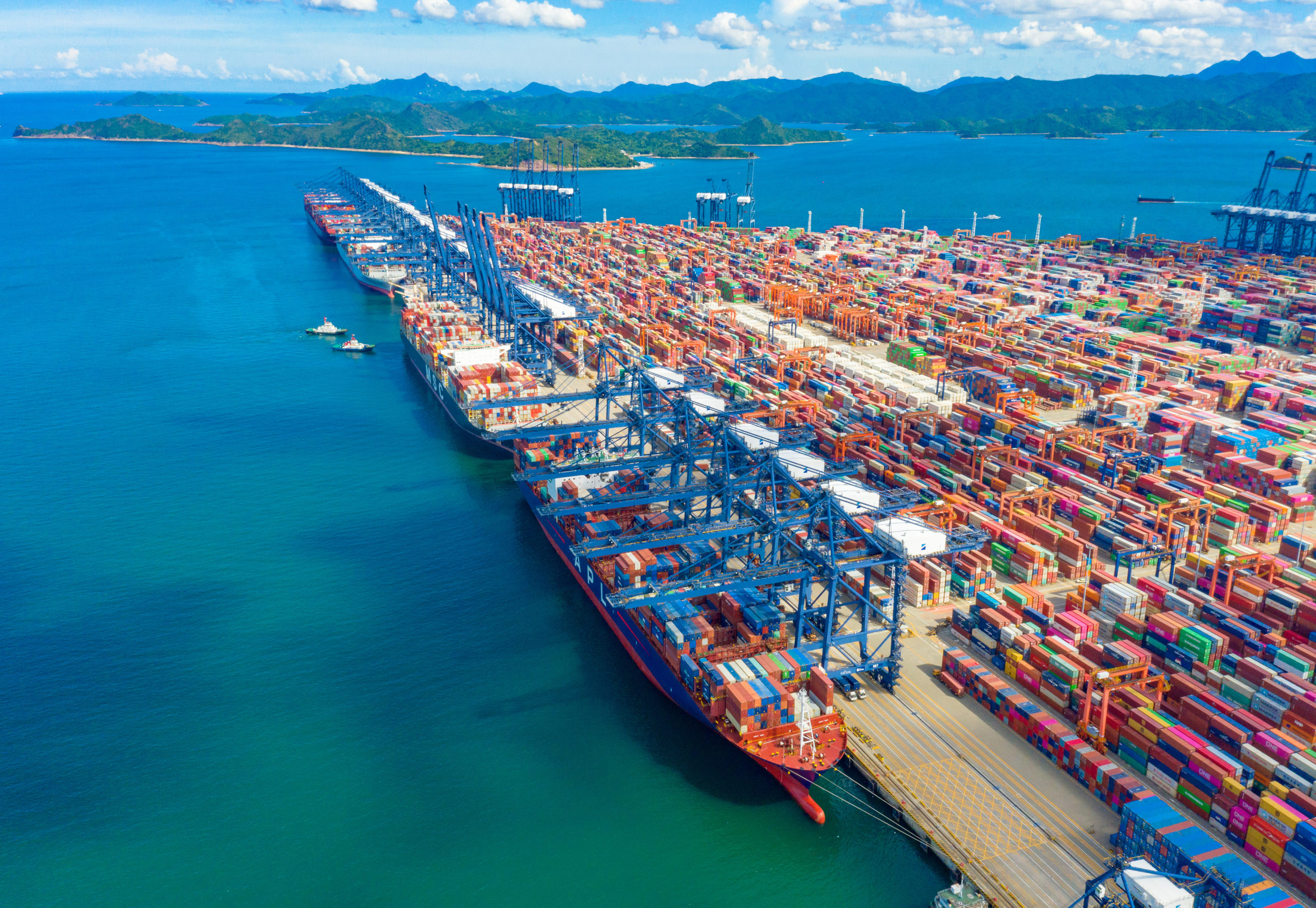
The congestion at Yantian port in China is giving industry experts headaches. One of the main issues arising out of this congestion is the inability to plan and deliver a coherent logistics service. This is one of the many disruptions that are expected in the shipping industry. This requires a need for planning and creative solutions.
Some experts have suggested that the Yantian congestion is even worse for the industry than the Suez Canal blockage which caused chaos this spring. Certainly, the Yantian problem is greater than the other congestion difficulties that are being faced at the Long Beach and Los Angeles ports. The sheer magnitude of the trade lanes means that the impact is bound to be felt far and wide.
Battering an already battered shipping industry
Whereas the Suez Canal issues were important and attracted a lot of media attention, they only impacted a limited number of regions. Yantian is a different matter since it acts as an export hub for the lucrative markets of North America, Europe, Oceania, and Latin America. This is an additional problem that is challenging an already overwhelmed industry that is dealing with new and unique challenges.
The shipping industry has suffered a few rough months, not in terms of demand but rather because of demand that exceeds supply. The logistics systems that are in place seem to be unresponsive to these challenges. The industry has had to contend with equipment shortages and customers are complaining about reduced reliability in terms of scheduling.
The statistics are simply not acceptable. For example, reliability for ferrying and picking up cargo on time is standing at as low as 5%. This is a drastic drop from the 80% minimum that was being touted in the previous year. Ocean carriers are introducing more and more blank sailings. Others are skipping ports to improve their reliability percentage.
Those shipments that are skipped today are going to the backlog of tomorrow. The problems keep piling up literally and figuratively. Until demand falls, these problems are bound to continue. Shippers, carriers, and logistics companies need to think of several potential solutions that might help them avoid the worst of the combined crises.
First Solution: Being open to realities of hyper flexibility
These are situations that call for a heightened level of flexibility since everything is unpredictable. Such flexibility may involve an overhaul of the internal organizational structure so that it is responsive to trends in the market. Consider the importance of being able to quickly switch ports if one is having insurmountable problems. Carriers need to manage their capacity creatively to overcome the long backlogs and shortages.
For a long time, the shipping industry was encouraged to improve its flexibility in preparation for the types of crises that it is facing today. If you are dealing with delays of 10 to 15 days at Yantian, it means that you are potentially losing weeks of your scheduling through idling. Typical waitlists are between two and seven days, so this is the time to act to bring back some parity to schedules.
One of the ways you can achieve flexibility is to switch your modes, ports, and trades depending on market conditions. This ought to be an active strategy that relies on information flows from the sector. The days of annual adjustments are over. The market is shifting too fast and those that are left behind will pay the cost. Any space that is available should be prioritized and used imaginatively to ship as many products as possible in the shortest period.
We have already seen this strategy in action when delays were reported at Los Angeles. The savviest carriers and shippers changed to the Port of Oakland. However, Oakland is now congested for this reason, and it makes sense to return to LA if it is a better option. Moreover, it is also possible to find an alternative port to work with. Those that remain faithful to Oakland are soon going to be stuck for weeks on end.
It is important to base any strategy on information. One of the facts now is that carriers are deploying mainly on the US West Coast (USWC). This is creating routing complexities as goods are brought into the interior. For example, there are reports of rail congestion and chassis shortages. Carriers are therefore limiting options for containers moving inland. Some shippers and carriers are leveraging their trucking and transloading connections to deal with the influx of containers terminating on the USWC.
Air freight remains a solution for the lighter cargo, bearing in mind its considerable expense when compared to shipping. There are certain goods that are just not right for air freight. A much more practical solution is to consider the mixing and matching of modes. For example, the use of LCL and air, depending on the products and the price that the customer is willing to pay.
Shippers and carriers should not limit themselves in the solutions that they choose. It is important to have the right partners to deal with any problem. Technology is another possible aid. Those that have the advantage of skill come to the bargaining table with an in-built competitive advantage. Ensure that you have a strong inland network to reduce the waiting times and delivery times for your customers.
Second Solution: Managing challenges through ultra-prioritization
In a crisis such as this, you must make tough decisions. Not every option is viable or urgent. Ensure that you have an understanding of shipping classifications and their implications for your business model. Take advantage of any picking opportunities that come your way. Above all, do not be afraid to abandon options that are showing signs of failure.
Companies that deal in seasonal items are particularly vulnerable when it comes to prioritization. Their selling window is limited, and they feel that they must stick with the old models to survive, regardless of the circumstances. The rationale is that there is an exceedingly small window in which customers are going to buy pools, and patio furniture for example. However, that does not mean you have to be everywhere and everything to everybody.
Whereas it is ideal to place top priority for all your shipments, be prepared to identify those top priority items that must be given precedence. The prioritization starts now so that when you are presented with options and a crisis, you can make the tough calls. LCL shipment is an example of an option where you allow specific parts of your shipments to go before others because they are ultra-priorities.
Third Solution: Make strategic use of historical data
Data is a key resource when managing these crises. The most successful players in the shipping industry are the ones that can reference their past to predict their future. It is imperative that you position yourself as an expert and the first to know when things happen. Cyclical patterns are a fact of life in this sector and that offers opportunities for learning.
It is a grave mistake to dismiss historical data as being old and outdated. There are companies that are looking back at 2 decades of big data to inform their current decision-making. All core trades have been shaken by the crisis of shipping so it might be a good idea to look in the rearview mirror to see what our predecessors did when faced with similar problems. The historical data is not just about the market, but also about how your business model has coped with adversity in the past.
Learning builds resilience. Things are bound to improve because they have improved before. A lot of critical information may be hidden in your archives. The key is to extract what you need and make it relevant to the situation you are facing today. For example, you may have survived before by changing your distribution centers and sourcing some services. Pick up those contacts and re-engage them.
Wrapping up
High demand for shipping services is not a temporary problem. It is here to stay. Rather than complaining about the negative impact, it has on businesses, think of new solutions. These include better prioritization, organization, management, flexibility, and learning.