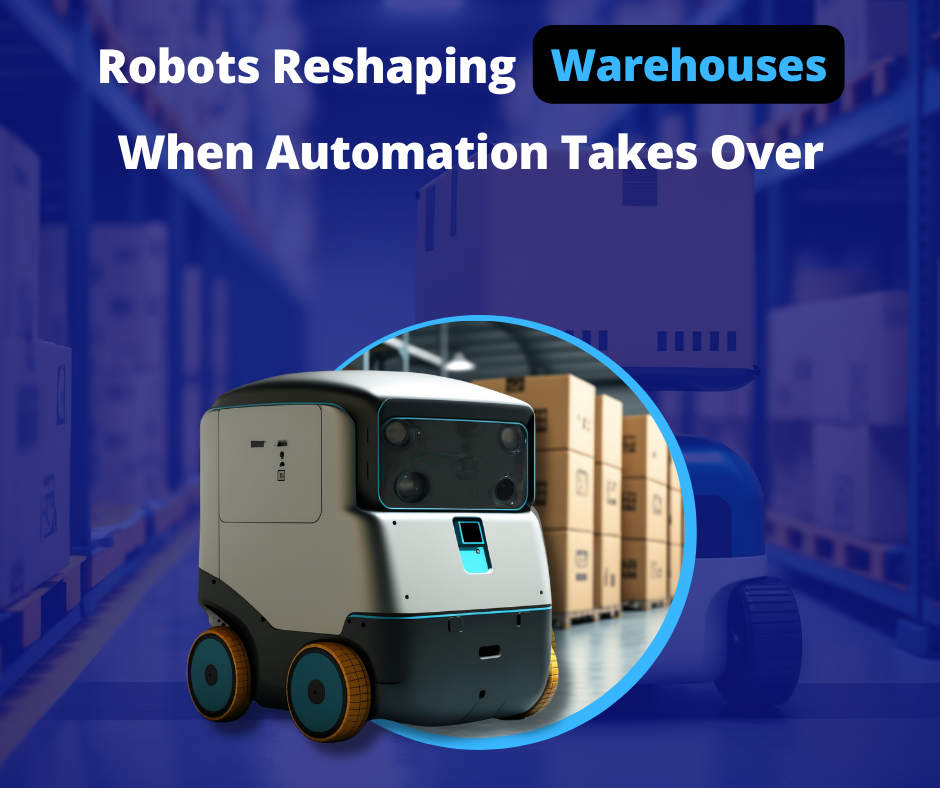
Navigating the Robotic Revolution: When Warehouses Go Automated
The rise of robots in warehouses is no longer a vision of the future; it’s a reality reshaping the logistics and supply chain landscape. Companies are increasingly investing in robotics solutions to automate various aspects of their warehouse operations. Robots are becoming integral to modern warehousing, from unloading trucks to material handling. In this article, we delve into the growing influence of robots in the warehouse and explore the implications of this transformation on the logistics and shipping industries.
The Robotic Revolution
The rise of robots in warehouses is no longer a distant future. Instead, it’s happening daily. Recent developments in the logistics and supply chain industries have showcased increased adoption adopting of automation and robotics to streamline warehouse operations. DHL Supply Chain’s significant investment of $15 million in Boston Dynamics’ robots demonstrates a commitment to automating warehousing processes. The introduction of Stretch, Boston Dynamics’ robot designed for unloading in distribution centers, marks a crucial step toward full automation. As part of DHL’s Accelerated Digitalization agenda, these robots are set to revolutionize warehouse operations, enhancing efficiency and reducing reliance on human labor.
Vecna Robotics’ successful Series C funding round, with $65 million raised, highlights the industry’s strong interest in automated material handling solutions. With millions of forklifts operating worldwide, there is ample room for growth in automating material handling processes, ultimately increasing throughput in warehouses and factories. Exotec’s $335 million in Series D funding showcases the demand for high-density inventory storage and retrieval solutions. The Skypod system’s use of robots that can reach heights of 36 feet promises to optimize storage space and improve retrieval efficiency across various industries.
Additionally, ArcBest Corp., NFI Industries Inc., and Phantom Auto Inc. have partnered to deploy remote-enabled forklifts. This alliance underscores the importance of remote operation technology. This innovation allows off-site operators to control equipment using video and audio streams, expanding the workforce’s reach and flexibility.
These investments and developments collectively signify the growing momentum toward warehouse automation. With the logistics and supply chain industries continuously evolving, embracing automation is no longer a matter of if but when for most companies. The need for efficiency, cost-effectiveness, and scalability will continue to drive the implementation of robotics and automation technologies in warehouses worldwide.
The Implications
Integrating robots into warehouse operations is not merely a trend; instead, it represents a strategic response to the evolving needs and challenges of the logistics and supply chain industries. The implications of this transformative shift are far-reaching and hold significant benefits for businesses and consumers alike.
a) Improved Efficiency: One of the most immediate and compelling advantages of incorporating robots into warehouses is the remarkable boost in efficiency. Robots excel at performing repetitive and labor-intensive tasks with unparalleled precision and consistency. For instance, robots like Stretch by Boston Dynamics can automate the unloading process, which traditionally requires manual labor. By expediting these essential functions, robots significantly reduce lead times, enhance order fulfillment speed, and optimize the overall workflow within the warehouse. Consequently, businesses can fulfill customer orders more swiftly, resulting in higher customer satisfaction and loyalty.
b) Mitigating Labor Shortages: The logistics industry is grappling with a persistent labor shortage, making finding and retaining skilled workers increasingly challenging. Robots reduce the industry’s reliance on human labor by taking on routine and physically demanding tasks, such as lifting and transporting heavy materials. This alleviates the pressure on businesses to constantly recruit and train new employees. Furthermore, robots work tirelessly around the clock, contributing to the continuity of warehouse operations even during peak demand periods or labor disruptions, such as strikes or pandemics.
c) Cost Savings: While the initial investment in robotics technology can be substantial, the long-term cost savings are often substantial. Robots enable companies to significantly reduce labor costs by automating manual tasks. Moreover, robots’ consistent and precise performance minimizes errors and product damage, resulting in lower operational expenses and reduced waste. Additionally, robots optimize resource utilization by efficiently organizing and managing inventory, contributing to cost savings.
d) Scalability As businesses experience growth and fluctuations in demand, robots offer a highly scalable solution. Unlike traditional workforce expansion, which involves recruiting, hiring, and training additional employees, robots can seamlessly adapt to changing workloads. During peak seasons, robots can be deployed to handle increased order volumes, ensuring that businesses meet customer demand without compromising quality or delivery timelines. When demand decreases, robots can be scaled back accordingly, preventing the underutilization of human resources and excessive labor costs.
The Current Landscape
The use of robotics in warehouses is a challenging process that depends on many variables, including the level of labor input, industry-specific standards, and the economic viability of automation. While robots are becoming increasingly prevalent in such conditions, the level of adoption varies significantly among companies and industries. A recent survey of supply chain professionals sheds light on this diversity in adoption rates.
Surveying Warehouse Automation Levels
According to the survey, a substantial portion of respondents indicated that their warehouses were either “Slightly Automated” or “Not Automated at All.” These results imply that many warehouses have not fully adopted automation or have only started down the road. This variation in automation levels is the result of a complex interplay of factors that affects how businesses make strategic decisions.
Industry-Specific Needs
One of the primary determinants of robotics in warehouses is the nature of the industry itself. Different industries have varying degrees of labor intensity and operational requirements, which influence the applicability and necessity of automation.
For instance, industries that rely heavily on labor-intensive activities, such as case picking in e-commerce or order fulfillment in retail, find it more conducive to implementing robotic solutions. In these settings, robots can excel at repetitive tasks, reducing the reliance on human labor and improving overall efficiency. As consumer demand for quick order turnaround and accurate delivery increases, industries like e-commerce have a strong economic incentive to adopt automation technologies like robots.
Economics of Automation
The economic viability of automation plays a pivotal role in adoption decisions. Companies evaluate the return on investment (ROI) in their specific context. This assessment considers the cost of implementing and maintaining robots versus the savings achieved through reduced labor costs, improved efficiency, and minimized errors.
For businesses engaged in labor-intensive activities where human labor costs are high, the case for automation becomes more compelling. Robots can substantially reduce labor expenses over time by automating repetitive and physically demanding tasks. This economic rationale aligns with adopting robots in sectors like manufacturing, where precision and consistency are paramount.
Modernizing Software Systems
While some industries prioritize investing in robots, others have alternative priorities. For example, some businesses focus on modernizing their software systems before fully embracing automation. Integrating robots into warehouse operations often requires seamless coordination with existing warehouse management systems (WMS) and order management systems.
In the past, legacy software systems posed challenges for companies seeking automation. Integrating robotic technology with outdated systems was often complex and costly. As businesses upgrade their technological infrastructure to more modern platforms, the feasibility of deploying robots becomes more attainable. This transition allows companies to consider and plan for automation as part of their long-term warehouse strategies.
Balancing Human and Robot Collaboration
Another consideration in adopting robotics is the balance between human and robot collaboration. While robots can perform numerous tasks efficiently, there are roles where human judgment, adaptability, and decision-making remain invaluable. Striking the right balance between human and robot capabilities is crucial for optimizing warehouse operations.
A company’s software systems’ current state, industry-specific needs, and economic considerations all have an impact on the adoption of robotics technology in warehouses. While some industries have fully embraced automation due to labor-intensive activities and strong economic incentives, others are gradually modernizing their infrastructure to prepare for future automation. Integrating robots into warehouses represents a strategic response to the changing landscape of logistics and supply chain operations, where efficiency, cost savings, and adaptability are paramount. Ultimately, adopting robots hinges on a company’s unique circumstances and strategic vision for warehouse optimization.
Wrapping Up
Robots undeniably transform the warehouse landscape, offering improved efficiency, cost savings, and scalability. However, the decision to implement robotics technology is not universal, and its timing depends on various factors. Whether they are driven by labor shortages or the need for cost-effective scaling, robots will continue to play a significant role in warehouse operations. For most companies, it’s not a matter of if but when they will adopt these technologies to stay competitive in an evolving industry. As robots become increasingly prevalent, the logistics and shipping industries will experience a fundamental shift, redefining how goods move through the supply chain.