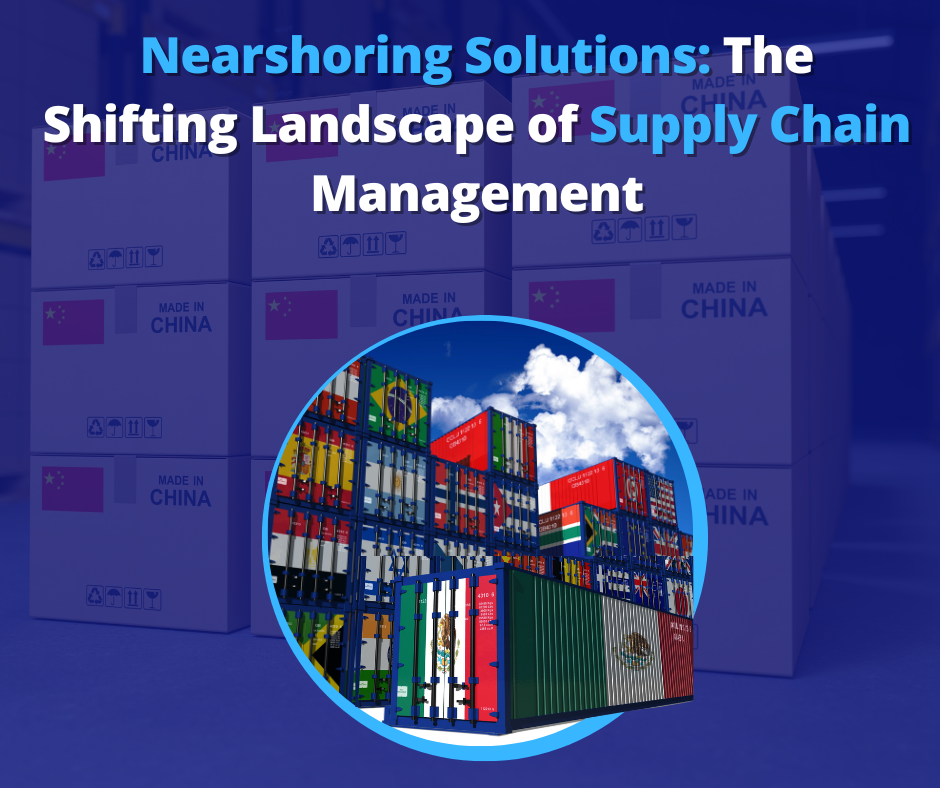
One of the emerging options for businesses when managing their logistics and supply chain is nearshoring. This approach brings production closer to the business, therefore avoiding many of the challenges that arise when transporting merchandise over long distances. The USA is no exception in this regard. However, moving facilities to Mexico or other nearby locations will inevitably raise questions about supplier networks, cost management, and logistical arrangements.
Companies explain their experiences of nearshoring
North American companies are contending with the reality that nearshoring is increasingly popular. Hence, new factories are being commissioned and constructed. Nevertheless, the shifts in the supply chain have created new challenges that were not always predictable in the beginning. A nearshoring business strategy necessarily requires a re-orientation in operations. That can be a challenge for businesses that were used to a different way of working in the past.
Premium Guard is a case in point. It expanded its factory in Mexico. However, that meant importing new equipment from Asia. This was premised on the reality that Asian manufacturers offered better pricing and quality options than other parts of the world, according to Roel Dekkers (Director of Supply in Mexico. This change has necessitated a new network of suppliers to work with Premium Guard, bearing in mind the need to create and distribute products to very precise specifications regarding packaging and delivery timescales.
The Chinese factor struggles to deal with the more competitive Chinese pricing strategy. Indeed, Mexico has less abundant raw materials, such as paper pulp and steel compared to China. This raises production costs and means Premium Guard must ultimately pay for the differences. Yet, the challenges are deemed worthy, given the new sourcing strategy not overly reliant on a single country that is removed from the company. Near sourcing is seen as a complementary measure to support existing supply chains in Asia. This is a lesson from the supply chain crises, which is being addressed through appropriate operational adjustments.
Learning from the logistical experiences of other companies
More companies are taking a leaf out of Premium Guard, a leading auto supplier. Their strategies reflect a deep understanding of the geopolitical dynamics of contemporary markets. Moreover, these businesses anticipate and understand distant supply chain’s inherent risks and uncertainties. Western countries once emphasized offshoring to control costs and deal with labor disputes at home. Instead, the vulnerabilities of the supply chain have forced companies to reconsider the option of nearshoring. Asia, generally, and China, specifically, is likely to lose out in terms of preferred manufacturing location for companies based in the West (especially North America and Europe).
The shift away from China started as far back as 2018 when the then-Donald Trump Administration in the USA slapped tariffs on China in addition to existing import duties on a range of goods. Many companies predicted some trade war and started making alternative arrangements, including nearshoring. The Covid-19 pandemic and the resultant disruptions to the supply chain resulted in an even more intense search for alternatives. The pandemic caused a significant contraction in shipping demand, but that quickly surged when restrictions were lifted.
Following the Covid-19 shutdown, important pressures on the shipping industry and logistics companies meant a rethink of strategy. For instance, the period was marked by product shortages, port bottlenecks, and a transportation infrastructure that was too vulnerable to deal with the demands. Meanwhile, budgets were shrinking in the corporate world as many braced from the embers of the Covid-19 economic upheavals. In these circumstances, nearshoring represented a sensible response.
Comment on finished oil filters at the Interfil plant
The production growth in the USA has mainly emanated from high technology sectors, including semiconductors. Meanwhile, the national priorities as defined by the Joe Biden Administration in the USA include self-reliance, supporting American business, and sustainability. Hence, billions of dollars have been injected into the economy to reduce its over-reliance on Chinese products. This, then, raises questions about the next best alternatives.
For the USA, the production in Mexico seems like a good option. It is geographically convenient and has the necessary labor force to support production. Indeed, Mexico can consistently manufacture goods at a much cheaper cost than the USA. Although not always as efficient as China’s production, Mexico can compete in this arena. Besides, Mexico has a free trade agreement with Canada and the USA, meaning it already has a foothold in the North American market. The implication is that there are fewer tariffs when you import from Mexico than from China.
Business leaders and owners in the USA are certainly looking to Mexico for solutions. Jake Ozmun (Director of Sourcing at Malouf Cos.) has commented on the fate of the Logan, Utah-based furniture retailer. He suggests that his company requires about 14 days to move merchandise from Mexico to Utah, about 30% of what would be required if imported from Asia. Therefore, it is unsurprising that the company currently sources 20% of its product from North America, with Mexico playing a significant part.
Mexico may not be a complete or faultless solution
Despite the attractions of nearshoring to Mexico, there are distinct and important disadvantages that should be considered when making this strategic decision. For instance, the electrical grid is not always as reliable as companies in the USA might want. Moreover, the lack of locally produced raw materials and parts means there is still a need to continue sourcing certain items from Asia. Chris Rogers (Head of Supply Chain Research at S&P Global Market Intelligence) argues that the risks of offshoring must be balanced with nearshoring to get the right perspective.
Mexico is not without its obvious challenges, a case in point being the drug cartels that have the power to cause havoc to the supply chain. Additionally, the fact of the U.S.-Mexico-Canada trade pact means that the trade union rights of Mexican workers are automatically boosted. That might imply that there is increasing industrial unrest in addition to the existing and perhaps unrelated problem of high crime rates. For companies looking for stability and predictability, this is not the kind of risk they want to encounter. Moreover, China is still a strong producer despite losing market share in exports to the USA in specialties such as apparel and electronics. Hence, its rivals in this area (e.g., Vietnam and Mexico) may not provide a completely foolproof solution.
The Chinese advantage remains
Many of the reasons that made China a manufacturing hub remain today, including the low cost of production. Since its accession to the World Trade Organization in 2001, China has strived to make itself attractive to business. There is a vast network of suppliers in a complex ecosystem that is hard to replicate elsewhere. Mexico is comparatively late to the game and cannot quickly overtake China in these respects. Omar Troncoso (Head of the Mexico City office for Kearney Inc.) sees some industrial parks focusing on home appliances, electronics, and furniture in Mexico.
Yet, nearly 50% of those investments are driven by Chinese entrepreneurs seeking to get close to the US border. Already, China is responding to the new challenge. Logistics and freight companies are flocking to the US-Mexico border to process the parts sent from Asia. Meanwhile, Niels Larsen (North American president of DSV A/S, a Danish forwarder) notes insufficient direct flights between Asia and Latin America. So, the company flies their parts to Arizona and California before tracking them to Mexico. Asia will always be part of the equation, at least for the foreseeable future.
Wrapping up
The upheavals of Covid-19 are still being felt in international trade, shipping, and logistics. One of the solutions proposed is nearshoring, with Mexico being a case in point for supplying the USA. However, it will take many more changes for China to be supplanted as the manufacturer of choice due to its complex ecosystem of supplies and lower production costs.