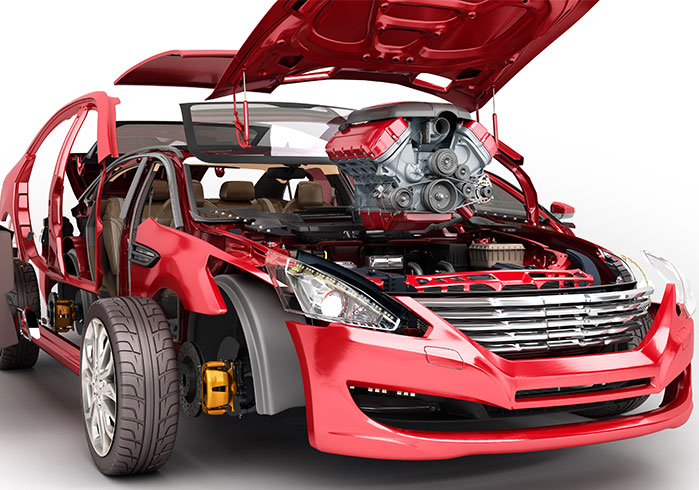
Right now the United States auto supply chain has seen a significant decrease in sales combined with tariffs. Together these two factors have driven imports down for the majority of 2019 and are likely to be the cause of radically changed patterns of consumption and behavior thanks in large part to the COVID-19 pandemic. This shift brings with it the potential for a long-term look at electric-powered vehicles.
Building resilience into supply chains
That said, everyone involved in these supply chains is looking to build resilience into them. US imports for autos and auto parts dropped 14.7% in 2019 compared to the same amount in 2018. In-vehicle components normally make up 5% of import trading for the United States and 7% of export trading with a total of 5.5% for all U.S. trade. But, these numbers are changing. There are many questions that the auto industry is facing especially with 2020 in full swing and changes taking place drastically within the economy and consumer purchasing habits. At this point, companies are asking themselves how they can build resilience within their supply chains and particularly how they can keep popular just in time fulfillment strategies and lean manufacturing intact on a large scale.
The outcomes of the changes to the economy and the shipping community at large are likely to reverberate not just throughout the auto industry and those involved therein but throughout the greater shipping community. As you start to unfurl one particular aspect of the economy, it seems that there are many more interrelated parts than one might think. These economic changes are being felt throughout the transportation industry and particularly affecting carriers and ports that were heavily reliant upon auto imports and exports for the majority of their traffic.
3D Printing and Fuel Marketing
Looking back at electric vehicles, the pace and scale of the industry become an important trend especially for those in the logistics who are looking to monitor where things might turn over the upcoming years and in what direction. Conventional drivetrains might have upwards of 2,000 individual components but electric vehicles can have as few as 20. More importantly, electric vehicles also have reduced dependence on transmissions, and transmissions accounted for 27,000 Import and Export TEU last year, comprising 1.3% of the entire auto trade for the United States. In terms of percentages, gearboxes made up another 1.5% of all imports and 1.1% of all exports for the United States. As people start to shift toward electric vehicles, it brings with it fewer parts and a significant potential drop in the demand for imports and exports throughout the supply chain even if the demand for autos and auto parts themselves increases.
In the current market, traditional parts suppliers are responsible for 70% of vehicle content share for the internal combustion engine but as people make the switch toward battery electric vehicles and that starts to shake over a larger percentage of the market share, international parts suppliers could see a drop-down to 28%. They are not the only ones who stand to suffer. Original equipment manufacturers like Hyundai or GM have about 20% of conventional vehicles right now and that could drop to 5% thanks to electrification. Moreover, there are 35 different categories for vehicle parts that are created and evaluated and when you compare a traditional vehicle to that of an electric vehicle, it’s anticipated that roughly 16 functions will continue to grow within those categories but 17 or going to face a serious decline and that means that the future business impact on those 17 declining functions and the remaining functions is uncertain.
As manufacturers start to change their current operation and move toward producing electric and autonomous vehicles, shippers and those involved in the auto industry need to be aware of the fact that there is going to be a great a reliance on additive manufacturing, specifically 3D printing. Right now 3D printing isn’t widespread but it’s going to become widespread when it’s responsible for printing things like vehicle frames and using its technology to produce critical and complex components. Additive manufacturing brings with it the opportunity for reduced waste material which is going to have a serious impact on export commodities for the United States, specifically metal and plastic waste.
Moving away from Just-In-Time (JIT) Manufacturing
Shippers are currently working to move away from just in time (JIT) manufacturing. Just in time manufacturing is unlikely to continue because of the weight of the components, the size, and the cost especially for things like vehicle engines. By moving away from just-in-time manufacturing, there will be an increase in capital expenditures. These strategies are not likely to be done away with entirely, it’s simply that cargo owners are going to evaluate what options they have to reduce their liability and give themselves more flexibility so within the confines of just-in-time manufacturing shippers are looking to take control of their cargo with whatever flexible opportunities they find.
Wrapping Up
Overall, shippers involved in the automotive industry and other professionals involved therein are looking to mitigate the impact of these economic changes, especially things like blank sailings and increased costs, as well as the shift within the industry toward electric vehicles and autonomous vehicles. A big part of that is being aware of what areas might make that significant jump, to what degree, and how shippers can plan for the impact that this will bring. In some cases, the impact might be a complete loss of imports or exports for pieces that are no longer necessary for electric vehicles, and in other cases, it might simply be a slight change in the way things are run. Either way, it’s important to be prepared.